Solar-powered steel processing innovations win award for PhD candidate
Swinburne PhD candidate Suneeti Purohit has won the 2019 AMP Amplify Ignite competition for her initiative to revolutionise the steelmaking industry by using solar power.
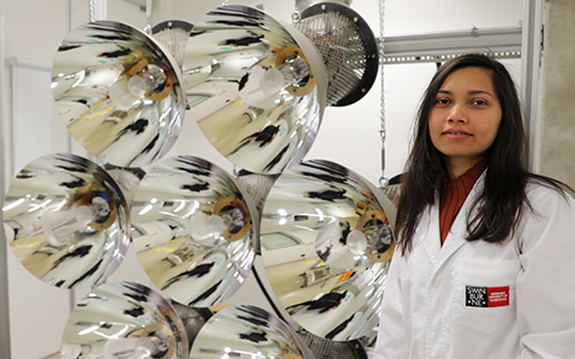
Australia is the world’s largest producer and exporter of iron ore, the basic ingredient in steel. However, for every tonne of steel made, twice the amount of carbon dioxide is produced.
In 2017-2018, global steel production was about 1800 million tonnes, accounting for about 30 per cent of total industrial carbon dioxide emissions.
“With my research, I am trying to lower carbon emissions by up to 50 per cent by following two novel approaches using concentrated heat from the sun to convert iron ore to molten iron” says Suneeti.
Two new approaches
The first approach involves using concentrated solar heat to substitute nearly 50 per cent of fossil fuels responsible for process heat generation during ironmaking.
“This concept has been tested in the laboratory-scale solar simulator-reactor setup at Swinburne and iron was successfully produced from iron ore,” Suneeti says.
The second approach towards curbing the carbon footprint is the development of an alternative agglomeration route of magnetite ore.
Currently, magnetite ore processing involves adding oxygen to oxidise magnetite to a better reducible hematite phase.
“This additional oxygen is subsequently removed during the iron ore reduction stage by burning extra carbon, which accounts for about 150 kg extra carbon emission for every tonne of iron production,” Suneeti says.
“We developed an alternative agglomeration process that involves forming lime-magnetite pellets that can directly be charged to iron making units without the need for oxidation.”
This work has generated two patents that have been filed in Australia and the USA.
“The great thing about this alternative agglomeration technology is that we are producing a desirable iron ore feed of magnetite at 300 to 400°C lower temperature than conventional iron ore agglomeration processes, which also makes this process suitable for solar application.”
As most of Australia’s iron ore mines are in the sunny regions of Western and South Australia, making use of intense sunlight on-site in the agglomeration process would not only save the cost of fossil fuels like coal and natural gas, but also save the transportation cost of the raw materials from mines to production sites.
“Currently, there is a strong push towards cleaner manufacturing technologies worldwide, Suneeti says. “My innovations have the potential to address these issues in an economical way.”